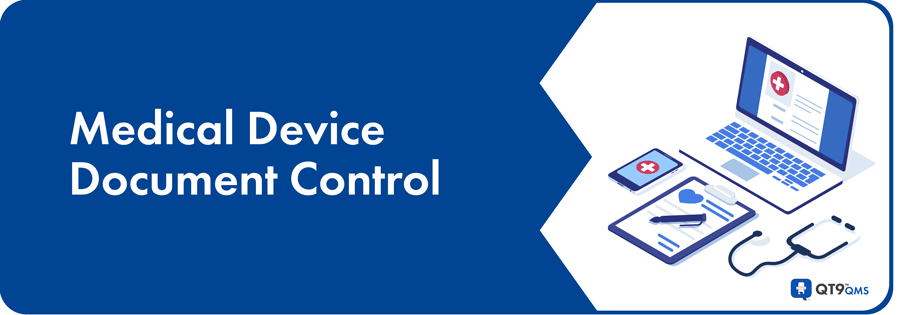
Importance of Automating Document Control for Medical Device Manufacturers
March 21, 2024
How do you do document control? If you’re a medical device company using manual methods for document management – spreadsheets, binders, email or even SharePoint – the first question is “Why?” If document control is so critical to strict regulatory compliance, why do so many medical device companies still use manual methods?
In a recent presentation, QT9 President Brant Engelhart challenged medical device companies to examine the effectiveness of their document control procedures and outlined how they can save time and money, better ensure compliance, and reduce risk by automating medical device quality processes with dedicated software from day one. We’ll give you an overview of this popular discussion and explore the best document control practices for medical device companies.
Defining document control
Let’s start with some definitions. Document control, also called document management, is the process that medical device companies use to ensure that important documentation is created, approved, revised, distributed, tracked and stored systematically throughout its lifecycle. Document control is a main component of many quality standards, with the goal being to demonstrate consistency and accuracy in operations.
Medical device document control regulations
The primary medical device document control standards are outlined in FDA 21 CFR parts 820 and 11, and ISO 13485. Current FDA standards are drawn from accepted Good Manufacturing Practice (GMP) guidance and require that procedures be in place for:
- Document approval – Documents must have a designated reviewer/approver, and approvals must be signed and dated.
- Document distribution – Documents must be available at all locations where necessary, and there must be a system to prevent unintended use.
- Document changes – Changes require review and approval by appropriate individuals and must be communicated in a timely manner.
ISO 13485 is the international medical device quality standard developed by the International Organization for Standardization (ISO). Compliance with ISO 13485 demonstrates an organization's commitment to ensuring the consistent safety, effectiveness and compliance of its medical devices. ISO 13485:2016 is the latest iteration of the guidelines and reflects many of the same document control elements as the GMP standards of ISO 9001. Requirements include:
- A system for document review and approval
- Records of revisions history and status
- Document availability at points of use
- Document legibility
- Document identification
- Control of external documentation
- Preventing deterioration or loss
- Preventing unintended use of obsolete documents
Fundamental document control uses in the medical device industry include work instructions, quality processes and procedures, specifications, drawings and labeling. Some of the required documents to be controlled by med device companies include:
- Quality manuals
- Standard Operating Procedures (SOPs)
- Design documents
- Test plans
- Validation checklists
If document control is so critical to strict regulatory compliance, why do so many medical device companies still use manual methods?
Manual medical device document control
Document control is the number one area for audit findings in both ISO and FDA audits. Even though document control is critical for FDA submissions, some companies still rely on manual methods, such as binders, Excel logs, Word forms, paper routings and email.
Major problems with manual document control:
- Susceptible to human error
- Laborious
- Time-consuming
- Lack of accountability
- Accessibility
- Disaster recovery
- Audit readiness
Manual and paper-based document control methods are cumbersome and inherently prone to errors, inefficiencies and compliance risks. Consider the following:
Accessibility
Both FDA 820 and ISO 13485 require that the most recent version of documents are available at points of use. What does this mean for your company? Do you use a network drive? SharePoint? Binders? With an eQMS, documents can be hosted in the cloud, which makes them available from a web browser on any device, anywhere, at any time with the proper login credentials.
Reviews and Approvals
How are you handling document reviews and approvals in your manual system? Are you using a manual word processing form that needs to be filled out and saved locally? How do you know who to route approvals to and how do you physically route the document reviews and approvals? Do you use manual signatures and then scan them into your internal systems? How do you know when to perform document reviews per document? An electronic document management system offers a host of tools to boost organization and accuracy, including routing documents for review, automatic email alerts for reviews and approvals, built-in electronic signature approvals, automatic tracking, and archiving.
Distribution and Training
How do you communicate document approvals or changes once finalized and made effective? Who do you train on the changes? Who creates and schedules the training? An eQMS automatically triggers training for named stakeholders and provides insight into who has or hasn’t completed the training.
Top reasons to automate medical device document control
You may believe that your document control processes are automated because you are using electronic applications. The difference between using “traditional” applications, like spreadsheets and email, is rooted in accuracy and efficiency.
With new technologies like an eQMS, document control is completely automated and connected, reducing the opportunity for human error and keeping quality tasks on track so users know where to find important documentation when it’s needed. eQMS software is geared toward compliance, making necessary compliance tasks a part of everyday processes. Below are a few of the features built into QT9’s QMS software that make automated document control superior:
Paperless Approval Routings with Electronic Signatures
Document control software easily routes documents to the appropriate individuals for approvals using email alerts and visual to-do lists and allows for FDA 21 CFR Part 11-compliant electronic signatures. Approval routings stay on track, letting you process compliance items faster and more accurately.
Online Collaboration
With eQMS software, it’s easy to get feedback on documentation changes before approval submission. Documents are centrally located in the QMS, and reviewers can access documents from any location. Automated messaging reminds users of review tasks and provides management with insight into review status.
Visual Document Relationships
Document control software users are able to establish document hierarchies, with parent or child relationships that are easy to identify when impacted by document revisions.
Automatic Training Links
Once document changes have been made and approved, QMS software can automatically trigger employee training, so training is initiated with the correct individuals.
Link to Quality Functions
Using document control in an eQMS allows you to link documents to other critical quality processes such as:
- Change control
- Audits
- Inspections
- Engineering changes
- Employee Training
- Product Design (design controls)
- Maintenance & Calibration
Link to Operational Functions
In addition, documents can be easily linked via operational function, such as:
- ERP
- Bill of Materials (BOM)
- Electronic Batch Record (EBR)
- Device History Record (DHR)
- Shop Floor Manager
- Master Batch Record (MBR)
- Device Master Record (DMR)
Improve Accessibility
Important documents are more accessible with a web-based central management system. Users are able to access documents from their computer, phone or tablet.
Involve Suppliers in Document Control
Whether it is sharing controlled documents with your suppliers or having customers sign off on spec changes, web portals make this easy.
Besides being able to simplify and organize processes in one place, dedicated eQMS software has built-in efficiencies. eQMS software automatically generates next steps in your quality processes, so tasks like risk assessments and supplier reviews are automatically generated. Users can also take advantage of useful aids, such as to-do lists, email reminders and automatic scheduling.
With an eQMS, you also have all of the most current data surrounding your quality operations in one place, helping you to make impactful decisions that are based on the most up-to-date information. Quality becomes ingrained in your operations and efficiencies are reached throughout your company, letting you bring products to market more quickly.
Conclusion
In the dynamic landscape of medical device manufacturing, effective document control is indispensable for ensuring regulatory compliance, maintaining product quality, and mitigating risks. By embracing automation technologies, manufacturers can revolutionize their document control practices, unlocking unprecedented efficiency, transparency, and agility. As the industry continues to evolve, leveraging automation will be crucial for staying ahead of the curve and delivering safe, reliable, and innovative medical devices that enhance patient outcomes worldwide.
QT9 QMS is a highly rated quality management solution with more than 28 modules that can help medical device manufacturers address FDA 21 CFR Part 820 and ISO 13485 now and under the new QMSR regulations in the future.