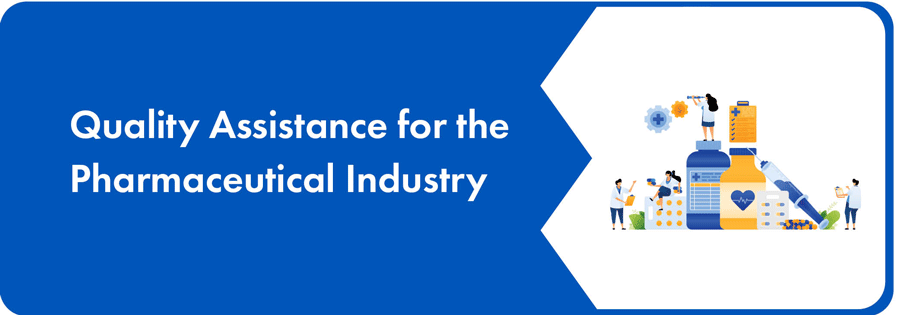
Introduction
What is quality assistance software?
Quality assistance for the pharmaceutical industry
Quality assistance for FDA-regulated pharmaceutical companies
Quality assistance for ISO- and GMP-regulated companies
Quality assistance for EMA-regulated pharmaceutical companies
How quality assistance software can help the pharmaceutical industry
Quality assistance for better audit outcomes
What is the best quality assistance software for pharma?
Quality Assistance Software for the Pharmaceutical Industry
February 1, 2024
A changing regulatory environment for the pharmaceutical industry has meant greater emphasis on risk management and quality control, calling on pharma to provide greater transparency and traceability at every step and for every player.
With all of the moving parts and the weight of end-user safety, it is no surprise that pharmaceutical manufacturers seek quality assistance to help ensure delivery of first-class pharmaceuticals that are compliant with EMA and FDA regulations.
Quality assistance software is helping pharma companies bring high-quality products to market faster by creating operational efficiencies and paving the road to regulatory compliance. We take a deeper dive into quality assistance solutions.
What is quality assistance software?
Quality assistance software is a system that helps organizations manage and document quality processes. Quality assistance systems include ISO 9001, Six Sigma and Total Quality Management (TQM).
A quality assistance system is a must for pharmaceutical industries managing EMA and FDA regulatory requirements. A quality assistance system enables organizations to centrally manage and document quality processes.
The most efficient quality assistance software automates, centralizes and streamlines tasks so that all GMP, EMA, FDA and ISO compliance standards are met and documented.
Quality assistance for the pharmaceutical industry
Regulatory guidance in the pharmaceutical industry focuses on the end user, emphasizing serving consumers at all stages - from the creation of medicines through market introduction, ongoing use and eventual discontinuation. Quality assistance programs must help pharmaceutical manufacturers meet regulatory standards at every step in the process.
Key ways a quality assistance program should support the pharmaceutical industry include:
- Automating workflows to ensure all procedures are followed
- Creating transparency and traceability
- Managing documentation and approvals
- Promoting total quality
- Centralizing and connecting risk management processes
- Ensuring suppliers adopt total quality and risk-based practices
- Fostering an environment of continuous improvement
- Utilizing real-time data
- Effecting management and employee engagement
Quality assistance for FDA-regulated pharmaceutical companies
FDA 21 CFR Part 211 is the primary standard outlining the steps for meeting minimum current good manufacturing practice (cGMP) standards for finished pharmaceuticals in the United States. Being able to meet its standards is required for FDA approval, with the goal of assuring that “the drug products have the identity, strength, quality, and purity they purport.”
FDA 21 CFR Part 210 is used in conjunction with Part 211. Where Part 211 focuses on process control for finished pharmaceuticals, Part 210 puts forth minimum standards for manufacturing, facilities and controls.
Meeting these FDA standards is a complex endeavor, but the major elements involve:
- Qualifications and skills of personnel
- Equipment and facilities maintenance
- Control of components, product containers and closures
- Production and process controls
- Packaging and labeling controls
- Warehousing and distribution
- Laboratory controls
- Records and reports
Quality assistance software can support pharma with the details of these elements by automating tasks such as training personnel, equipment calibrations, document management, risk management and inspections.
Quality assistance for ISO- and GMP-regulated companies
ISO 9001: 2015 ISO 9001 is an international quality management standard that promotes the process approach, which is based on the premise that consistent and predictable results are best achieved when individual tasks are managed as a function of a total, coherent system. To address this standard, the best quality assistance program should automatically manage each step in the process, including planning, implementing and assessing quality processes.
ISO 17025 ISO 17025 is the international standard that targets laboratories and their ability to demonstrate that they operate competently and generate valid results. Quality assistance efforts, such as providing a framework for safety and testing, are critical to pharmaceutical quality management.
GMP Good manufacturing practices (cGMP in the United States) is another global set of standards that promote risk-based quality management methods based on real-time data insights. This means quality assistance programs should help pharma companies identify, assess and mitigate potential risks that may affect the product and ultimately users.
Quality assistance for EMA-regulated pharmaceutical companies
EMA guidelines for the quality of pharmaceuticals in EU member states are provided for all stages of a pharmaceutical’s life cycle, with ICH Q8, Q9 and Q10 acting as the main drivers for development, manufacturing and risk management.
The guidelines were developed by The International Council for Harmonisation of Technical Requirements for Pharmaceuticals for Human Use (ICH), which was established in 1990 by regulatory and industry bodies from Europe, the United States and Japan in an effort to streamline pharmaceutical regulations in an increasingly global market.
ICH Q10 provides a model for an effective pharmaceutical quality management system. ICH Q10 is being looked to more and more by those creating pharmaceutical quality processes as it provides in one model what is addressed in both ISO and GMP quality guidelines and standards.
Any advanced quality assistance software provides solutions to address every aspect of ICH Q10, Q9 and Q8 as part of a total quality management solution.
How quality assistance software can help the pharmaceutical industry
Quality assistance software can automate and streamline multiple quality processes into one, integrated solution for the pharmaceutical industry. With an advanced quality assistance software, you can automate and centralize key activities, such as:
-
Document control
-
Risk management
-
Employee training
-
Measurement and testing
-
Inspections
-
Corrective and Preventive Actions (CAPAs)
-
Supplier management
-
Customer feedback
-
Electronic batch records
-
Inventory control
-
Management review
-
Regulatory compliance
Let’s take a closer look at quality assistance software capabilities.
Document management with electronic signatures Document management, or document control, centralizes documentation in one place. FDA 21 CFR Part 11-compliant electronic signature approvals make it possible to approve electronic records.
-
Centralize and organize documents so they are easily accessible anytime, from anywhere
-
Provide version control to ensure the latest information is used
-
Have full transparency and traceability with an electronic timeline of document changes
-
Utilize electronic review and approval with electronic signature compliance
-
Control access
-
Trigger training related to document changes
Automated employee training supports regulatory compliance and promotes a culture of quality by connecting quality system changes to employee training events. Training can be created using the software and assigned based on job duties. Employees get email prompts and reminders to complete training, and management gets a real-time view of employee training progress.
Risk management applications in QMS software allow you to harness your data to identify and monitor potential risks, automating associated tasks such as creating, evaluating and reporting on risk assessments. Risk assessments are integrated from a variety of additional QMS applications generally included in the software, such as corrective actions and engineering change requests (ECRs).
Equipment and facilities maintenance requirements can be automated with QMS software. Instrument calibration applications can generate maintenance schedules, reminders and reports to produce a verifiable audit trail, confirming your equipment has been properly maintained. Laboratory SOPs can be created, maintained and updated in the software, and training initiated to address changes or corrective actions as necessary.
Corrective and preventive action (CAPA) management is necessary under ISO and GMP standards for nonconformances, deviations, customer complaints, audit findings and recalls. QMS software provides tools to manage all your CAPA processes, from root cause analysis to approvals and verification of effectiveness.
Customer feedback A good quality assistance QMS solution also provides customer feedback tools that can integrate with the rest of your quality management system. Automated customer feedback lets you digitally track customer complaints and other communication so you can chart and trend findings and link to CAPA or risk management.
Supplier management is a key component of a modern quality management program and quality assistance software should offer automated supplier workflow solutions, such as supplier evaluations, data mining and trending, and communication, especially as pharma takes on greater responsibilities for these inputs.
Quality assistance for better audit outcomes
Besides satisfying for regulatory compliance details, quality assistance software provides you with a solid foundation for facing audits confidently by ensuring that the necessary documentation is in place, risks are managed, corrective actions are taken when needed and a culture of continuous improvement is fostered.
QMS software can greatly simplify the audit process. Records can be easily accessed through the system and shared with auditors, cutting the time you have to spend in the audit room and letting you get back to business.
What is the best quality assistance software for pharma?
The best quality assistance software for the pharma industry maintains or improves the quality of pharma products and promotes speedy delivery to consumers. Beyond standard quality management capabilities, such as document control, additional things to consider:
Validation – Pharmaceutical manufacturers should look for a validated quality assistance software. Validated systems ensure that the software is in line with requirements set forth in FDA 21 CFR Part 11, Part 210 and Part 211. Using a pre-validated platform gives life sciences companies upfront knowledge that this requirement is already taken care of.
Scalability – Look for quality assistance software that offers the ability to grow within the platform. While you’ll likely need document control from the start, other functions, such as automating supplier management, might be something you don’t currently need but can foresee being an asset as your business evolves.
Out-of-the-Box Capabilities – Many quality assistance software providers offer customization, which takes costs to a whole new level. Out-of-the-box quality assistance software can provide robust capabilities for less cost and generally mean quicker implementation.
Data storage — Consider how much data the platform is able to store for your company or if there are costs associated with different levels of data storage. Cloud-based data storage should be accessible at anytime and from anywhere.
Data mining – Being able to access real-time data helps you make evidence-based decisions for moving forward. Quality assistance software should offer the ability to access up-to-date data and ways to mine data to simplify analysis.
Summary
A continually changing market and new directions in regulatory compliance for pharmaceutical manufacturing calls for quality assistance that can streamline and centralize operations while providing integrated quality controls with full traceability. If that seems like too much to ask for, be assured that it is possible.
Quality assistance software can provide quality assistance that helps you bring consistently excellent pharmaceuticals to market in the most efficient way possible, focusing on the details so you can manage the big picture.
QT9’s highly rated QMS offers 25+ standard quality assistance modules, backed by full customer support and training, an available ERP integration and Business Intelligence tool.